Waste management according to Lean principles
A Lean approach to waste management helps minimise waste management processes that do not create value. Lean waste management thus saves most companies huge amounts of time, space and costs.
Inefficient waste management practices disrupt workflow and increase risks in many businesses
Inefficient waste management practices Many businesses commonly use small bins scattered throughout the premises to collect waste and recyclables such as cardboard and plastic, indicated by small blue dots in the image to the right.
This waste is then collected and moved outside for further sorting and processing, which may include folding or cutting, before being placed back into larger containers or compactors.
Such practices disrupt workflow and lead to inefficiencies. They also increase the likelihood of internal accidents and mis-sorting, particularly when materials are transported by forklift truck (FLT).
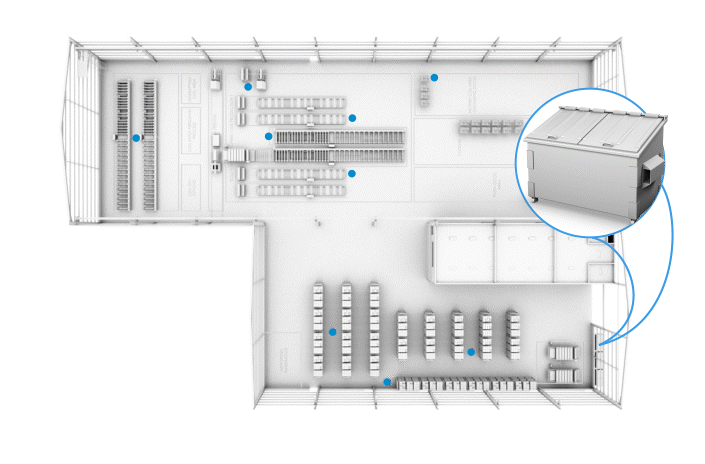
Numerous drawbacks exist with the use of standard waste containers in businesses:
- Considerable time is lost moving materials to the external container area and loading them.
- Uncompacted cardboard and EPS (Polystyrene) consume excessive space, leading to the need for more containers or costly waste pickups.
- Regular collection fees apply, even if the containers are not full when emptied.
- Misplaced materials in wrong containers lead to incorrect sorting, incurring additional costs.
- Significant increase in Carbon Footprint.
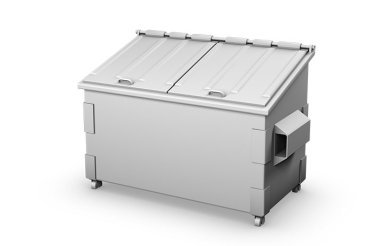
The Lean methodology aims to streamline workflows by eliminating unnecessary processes, reducing both internal and external travel, and continually making improvements.
While prevalent in industrial environments, lean practices are also highly beneficial across various other sectors.
Benefits of Lean waste management
Mil-tek incorporates Lean principles in customizing waste solutions. Our waste management systems are designed around Lean principles, positioning our air-driven compactors at the waste generation points, ideally near unpacking areas as depicted in the adjacent image.
This setup allows waste to be immediately processed in a cardboard or plastic baler without the need for folding or transporting it to another container. In the baler, waste is compacted by up to 90%. When the baler signals that it is full, the bale is safely and easily removed. These compacted bales are convenient for storage and later recycling.
Implementing Lean waste management leads to significantly more efficient workflows, saving substantial time, space, and costs on containers and waste collection.
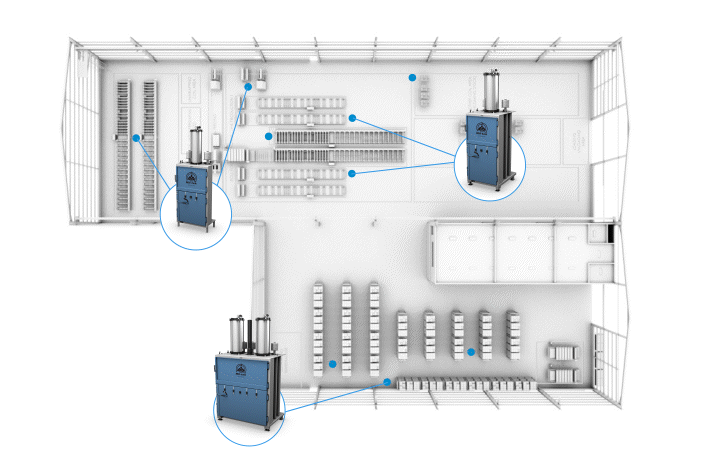
Enhancing safety and efficiency: Lean waste management reduces forklift use
Forklift Truck (FLT) related accidents are common and often have severe outcomes. The risk of FLT accidents increases in areas where pedestrian and vehicular paths intersect, especially if these areas are cluttered.
Adopting a Lean waste management system that compacts waste at its source can drastically cut down on FLT usage, enhancing safety significantly.
Achieve a 10:1 reduction in truck trips
Compacting materials before transport allows each trip to carry ten times more material. This reduction in trips lowers the risk of accidents, boosts efficiency, and cuts costs.
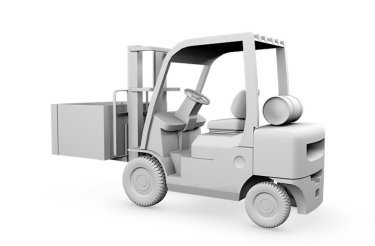
Four essential Lean principles
“Kaizen” – Continuous Improvement
This principle focuses on ongoing improvements that involve the entire team. Many organizations implement ‘Kaizen boards’ to track and enhance the development of new ideas for better efficiency.
“8 Types of Waste”
Remember the acronym TIMWOODS to identify the eight sources of waste: Time, Inventory, Motion, Waiting, Overproduction, Over-processing, Defects, Skills.
“Value Stream Mapping”
This involves mapping out production flows or other processes to pinpoint potential improvements and efficiencies.
“5S” – System and Order
The steps include Sort, Set in Order, Systematic Cleaning, Standardize, and Self-discipline. Employing 5S leads to improved ergonomics, a better working environment, higher quality, time savings, increased productivity, and enhanced employee well-being.
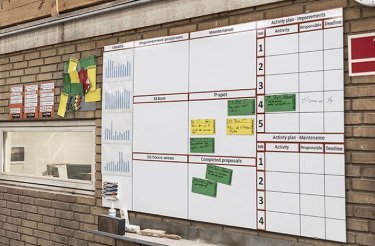
Are you interested in optimizing your waste management using the Lean approach and achieving significant benefits and savings?
Fill out the contact form here, and we will get back to you shortly.