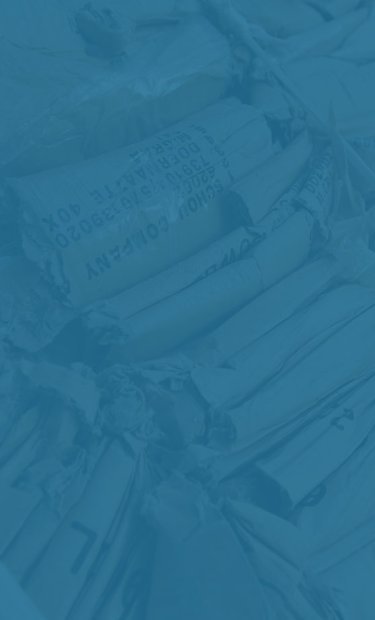
What Distinguishes a Hydraulic Baler from a Pneumatic Baler?
Our guide will help you understand the differences between hydraulic and pneumatic balers for recycling.
Choosing between a pneumatic or hydraulic baler
When you choose to install a recycling baler at your business premises, one of the decisions you’ll need to make is whether to opt for a hydraulic or pneumatic baler.
Both types of machines perform the same essential function: compressing recyclable materials such as paper, cardboard, and plastic into dense bales that are easy to transport and recycle.
The primary differences between pneumatic and hydraulic balers lie in their mechanisms and applications!
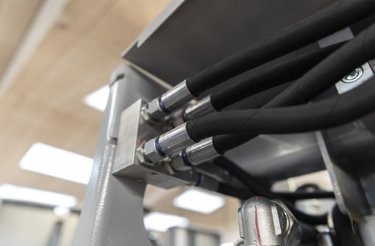
Pneumatic balers and their mechanisms and applications
These balers operate using compressed air to generate force. An air compressor supplies the necessary pressure, which drives the piston to compress materials. Pneumatic balers are generally more straightforward in design, with fewer components, making them easier to maintain and repair.
These are best suited for smaller operations and lighter materials, such as paper, cardboard, and plastic. They are often used in environments where the volume of recyclable material is moderate, and the focus is on ease of use and maintenance.
Known for their simplicity and lower initial cost, pneumatic balers are easier to set up and operate. They tend to be quieter and more energy-efficient for small to medium-scale recycling needs.
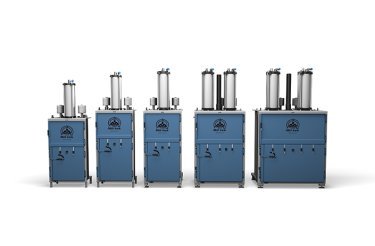
Hydraulic balers and their mechanisms and applications
In contrast, hydraulic balers utilize hydraulic fluid to create pressure. A hydraulic pump generates force by moving the fluid through cylinders, which in turn drives the pistons to compress materials. Hydraulic systems are typically more powerful, capable of exerting greater force, and thus can handle denser and more substantial materials.
These balers are ideal for larger-scale operations and heavier materials, including metals, dense plastics, and industrial waste. They are preferred in settings where high compression force is required to handle substantial volumes of heavy-duty materials efficiently.
While more complex and expensive, hydraulic balers offer superior performance in terms of compression force and capacity. They are more versatile and can manage a broader range of materials, making them suitable for heavy-duty recycling tasks.
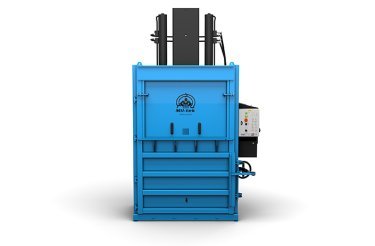
“Pneumatic Balers use compressed air to depress the pressing plate. Hydraulic Balers pump hydraulic oil to the pressing rams to generate pressure to the pressing plate.”
Pneumatic vs. Hydraulic balers: Further considerations
Both of these baler types can help your business manage waste efficiently. Each has benefits that are better suited to one particular business or another.
In summary, the choice between a pneumatic and a hydraulic baler depends largely on the specific recycling needs, the type and volume of material being processed, and the operational scale of the recycling facility.
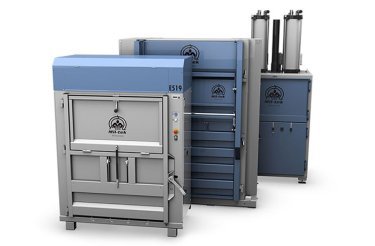
Here are several additional factors to consider when comparing hydraulic and pneumatic balers:
- Volume: Hydraulic balers are ideal for handling high volumes, typically more than one ton per week.
- Size: Pneumatic balers are generally more compact, making them suitable for spaces with limited room.
- Noise: Hydraulic balers tend to be noisy, so they are often placed away from production areas. On the other hand, pneumatic balers are quieter and can be located closer to the production line.
- Maintenance: While both baler types need annual maintenance, pneumatic balers usually require less upkeep since they have no electrical components.
- Power Source: Pneumatic balers can be connected directly to existing air lines, or a small compressor can be used if necessary.
- Power: Pneumatic balers lock the pressing plate in place using compressed air, while hydraulic balers need continuous power to maintain pressure.
- Strength: Hydraulic balers apply more downward force on materials due to the high pressure of hydraulic oil, although this results in higher power consumption.
- Hygiene: Pneumatic balers are better suited for food production facilities as they reduce the risk of contamination.
Have questions or need assistance?
We’re here to help! Please fill out the form, and a member of our team will get back to you as soon as possible.
Thank you for reaching out!